AI in Preventive Maintenance: Revolutionising Manufacturing Industries
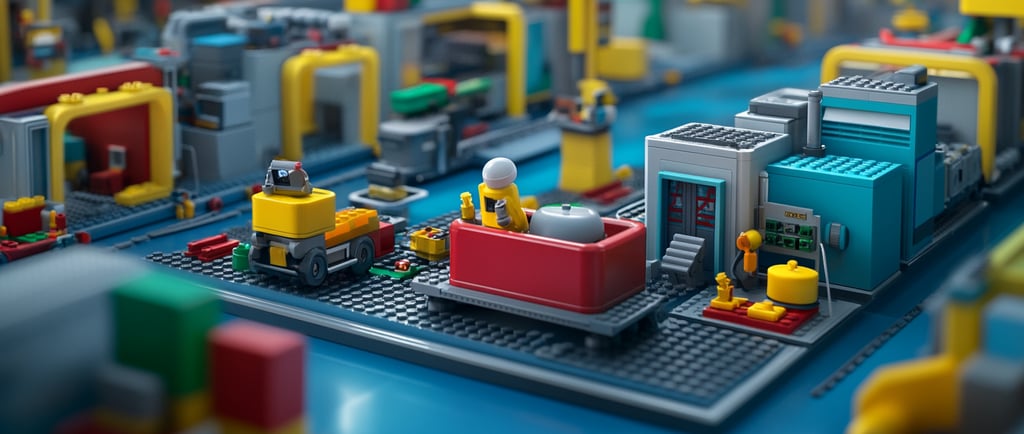
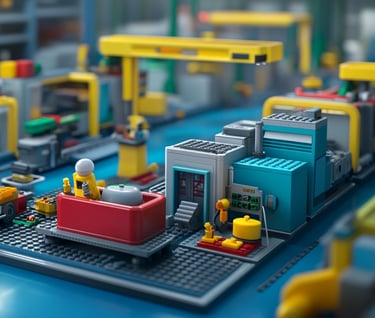
Imagine a world where machines could predict their failures before they happen, maintenance schedules are dynamically adjusted based on real-time data, and unplanned downtime is a thing of the past. Welcome to the era of AI-driven preventive maintenance, a revolutionary approach transforming manufacturing industries worldwide. In this article, we'll delve into the fascinating world of AI in preventive maintenance, exploring its benefits, real-world applications, and the future trends shaping this rapidly evolving field. From predictive analytics to automated maintenance schedules, join us as we uncover how AI is revolutionising how we approach maintenance in the manufacturing sector12345.
Understanding Preventive Maintenance
The Evolution of Maintenance Strategies
Understanding the evolution of maintenance strategies is essential to appreciating AI's impact on preventive maintenance. Traditionally, maintenance has been approached in two primary ways: corrective and preventive.
Corrective Maintenance: This reactive approach involves fixing issues only after they have occurred. While it may be quick for simple problems, it often leads to unexpected downtime and higher repair costs in the long run.
Preventive Maintenance: This proactive approach is based on scheduled or usage-based maintenance tasks designed to prevent failures before they happen. It relies on historical data and manufacturer recommendations to determine when maintenance should be performed4.
The Limitations of Traditional Preventive Maintenance
Despite its proactive nature, traditional preventive maintenance has its limitations. It often relies on fixed schedules and assumptions, leading to inefficiencies and waste. For instance, equipment may be serviced too frequently, leading to unnecessary downtime and costs, or not frequently enough, resulting in unexpected failures7.
Enter AI: The Game Changer in Preventive Maintenance
What is AI-Driven Preventive Maintenance?
AI-driven preventive maintenance leverages advanced algorithms, machine learning, and data analytics to predict equipment failures, schedule timely maintenance, and optimise operational efficiency8. By analysing vast amounts of data from equipment sensors, AI can provide real-time insights into machine health, detect anomalies, and predict failures before they occur1.
The Power of Predictive Analytics
At the heart of AI-driven preventive maintenance is predictive analytics. This involves using machine learning algorithms to analyse historical and real-time data, identifying patterns that indicate potential failures. By predicting when and where failures will likely occur, AI enables proactive maintenance, reducing downtime and maintenance costs3.
Real-Time Monitoring and Automated Schedules
AI technology enables real-time monitoring of equipment, allowing for automated maintenance schedules. Sensors installed in machinery continuously collect data, which AI algorithms analyse. These algorithms can then predict potential failures and schedule maintenance tasks at the optimal time, ensuring that equipment is serviced when it's genuinely needed35.
Implementing AI in Preventive Maintenance
The Role of IoT and Data Collection
Implementing AI in preventive maintenance begins with data collection. The Internet of Things (IoT) plays a crucial role here, with sensors embedded in machinery collecting vast amounts of data on equipment performance. This data is then transmitted to AI systems for analysis25.
Integrating AI with Existing Systems
To integrate AI with existing maintenance systems, assessing current processes and identifying areas where AI can add value is essential. This may involve upgrading legacy systems to ensure they can handle AI's data requirements. It's also crucial to ensure that data is high-quality and accessible for analysis9.
Training and Skills Development
Successful implementation of AI in preventive maintenance requires a skilled workforce. This involves training maintenance teams on how to use AI tools and interpret the insights they provide. Continuous learning and development are essential to keep pace with the rapidly evolving field of AI9.
Case Studies: AI in Action
Manufacturing Industry
In the manufacturing sector, AI-driven preventive maintenance has significantly improved operational efficiency and reduced downtime. For example, a leading automotive manufacturer implemented AI to monitor its production lines, resulting in a 30% reduction in unplanned downtime and a 20% increase in overall equipment effectiveness (OEE)2.
Oil and Gas Industry
The oil and gas industry has also seen substantial benefits from AI in preventive maintenance. Using AI to predict equipment failures, companies can avoid costly shutdowns and ensure continuous operation. For instance, an oil refinery used AI to monitor its pumps, leading to a 40% reduction in maintenance costs and a 50% decrease in unplanned downtime6.
Fleet Management
In fleet management, AI is transforming the approach to maintenance. Predictive analytics can analyse data from vehicle sensors, predict potential failures, and schedule maintenance tasks at optimal times. This has improved fleet efficiency and reduced operational costs3.
The Future of AI in Preventive Maintenance
Emerging Trends
As AI technology continues to evolve, several trends are emerging in the field of preventive maintenance:
Edge Computing: This involves processing data closer to where it is collected, reducing latency and enabling faster decision-making. It's beneficial in environments where real-time data analysis is critical.
Digital Twins: These virtual replicas of physical assets can simulate equipment performance under various conditions. Companies can use digital twins to test different maintenance scenarios and optimise their strategies without risking actual equipment5.
Augmented Reality (AR): AR is being used to provide maintenance teams with real-time information and guidance during maintenance tasks. This can improve the accuracy and efficiency of maintenance work.
Overcoming Challenges
While AI's benefits in preventive maintenance are clear, challenges must also be overcome. These include ensuring data quality, integrating AI with legacy systems, and developing the necessary skills within maintenance teams.
Statistics & Tables
To comprehensively understand AI in preventive maintenance, let's delve into some rich statistical data and visualise it using an HTML5 page with a responsive, full-width table. This table will utilise semantic HTML elements and embedded CSS for a visually appealing layout. Additionally, JavaScript functions will enhance table responsiveness, ensure mobile readability, add alternating row colors, include a fixed header, and enable column sorting.