Applying Data Analytics in the Manufacturing
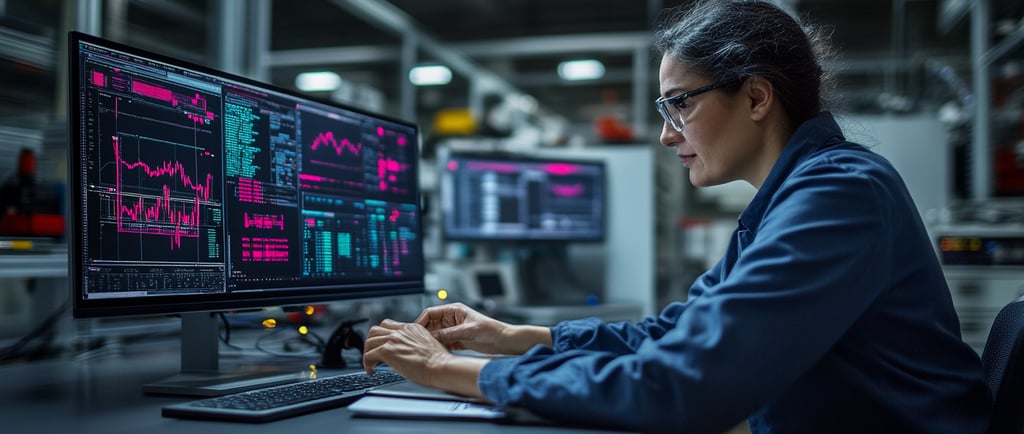
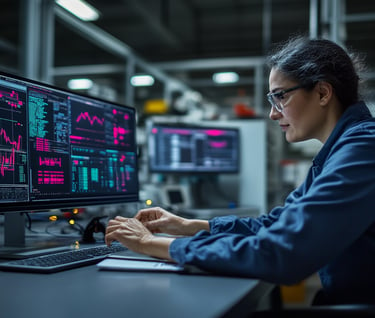
Integrating data analytics in manufacturing has brought significant advancements, offering real-time insights, process improvements, and predictive maintenance. By leveraging data analytics, manufacturers can streamline warehouse operations, improve demand forecasting, enhance quality control, and achieve end-to-end visibility. This integration has become even more crucial in the face of challenges such as the COVID-19 pandemic, which has intensified the need for efficiency and agility in manufacturing.
The industry has witnessed significant advancements in recent years due to integrating data analytics into manufacturing processes. By leveraging the power of data analytics, manufacturers can uncover valuable insights, optimise operations, and ultimately improve efficiency across the board. The industry is experiencing a rapid transformation, integrating advanced technologies such as data analytics. This integration has revolutionised manufacturing processes, enabling companies to achieve unprecedented efficiency, quality, and innovation.
What is Data Analytics?
Data analytics refers to data sets to uncover patterns, correlations, and insights that can drive informed decision-making. When applied to manufacturing, data analytics enables organisations to transform raw data from various sources, such as equipment sensors, production lines, and manufacturing, examining vast data sets to uncover patterns, correlations, and insights that can drive informed decision-making. When applied to manufacturing, data analytics enables organisations to transform raw data from various sources, such as equipment sensors, production lines, and supply chain, into actionable intelligence. By analysing this data, manufacturers can identify inefficiencies, spot trends, predict maintenance needs, and optimise resource allocation, improving efficiency and reducing costs.
In manufacturing, data analytics involves examining extensive data sets to reveal patterns, correlations, and insights that drive informed decision-making. This process transforms raw data from various sources, such as equipment sensors, production lines, and the supply chain, into actionable intelligence. By analysing this data, manufacturers can identify inefficiencies, predict maintenance needs, and optimise resource allocation, improving efficiency and reducing costs.
Manufacturing analytics is vital to modern manufacturing, enabling real-time insights, process improvements, and predictive maintenance. It involves capturing, cleansing, and analysing machine data to predict future use, prevent failures, forecast maintenance requirements, and identify areas for improvement. Manufacturing analytics is a critical step for manufacturing digital transformation required for Industry 4.0, which aims to automate traditional manufacturing processes, reduce costs, and improve efficiency.
The benefits of data analytics in manufacturing include more accurate demand forecasting, improved quality control, more efficient inventory management, and accurate end-to-end visibility. The use cases of manufacturing analytics range from demand forecasting and inventory management to predictive maintenance, risk management, price optimisation, and order management. While the potential benefits of data analytics in manufacturing are significant, its successful implementation requires careful consideration of data management, domain expert involvement, process and culture change, and modern data analysis tools. Additionally, using technologies such as robotic process automation (RPA) and the Internet of Things (IoT) can further enhance the capabilities of manufacturing analytics12345.
Key Use Cases of Data Analytics in Manufacturing
Predictive Maintenance
Predictive maintenance is a critical application of data analytics in manufacturing. It enables organisations to identify potential equipment failures before they occur. By analysing sensor data from machines and equipment, manufacturers can schedule maintenance during downtime, reducing the impact on production and improving overall efficiency. This approach also helps reduce repairs, replacement parts, and lost productivity costs.
Predictive maintenance leverages a combination of data elements, such as AI technology and the Internet of Things (IoT), to continuously analyse equipment conditions and predict maintenance needs. It monitors information from machines and devices to predict when and where maintenance will be needed, allowing organisations to detect abnormalities throughout machine operation and send instant alerts to the appropriate personnel16.
The benefits of predictive maintenance in manufacturing include reduced downtime, increased productivity, lower maintenance costs, improved equipment reliability, and enhanced safety for maintenance personnel. This approach also offers cost savings through improved uptime, reduced costs associated with unnecessary parts replacement, and greater efficiencies16.
Implementing predictive maintenance in manufacturing presents challenges, including obstacles to data volume, change management, and business model. However, by overcoming these challenges and leveraging the power of predictive maintenance, organisations can maximise asset availability, optimise maintenance tasks in real time, and avoid disruption to operations16.
Quality Control
Data analytics in manufacturing enables organisations to identify quality issues in real-time by analysing production data. This process allows manufacturers to detect anomalies in the production process, such as variations in product quality or unexpected changes in equipment performance, and take corrective action quickly. By examining historical production data, manufacturers can identify patterns and trends that correlate with defects, enabling them to pinpoint specific areas of improvement and implement targeted strategies12.
Data analytics in manufacturing offers substantial benefits for improving product quality and reducing defects. It offers more accurate demand forecasting, improved quality control, efficient inventory management, and true end-to-end visibility23. Predictive analytics can enable manufacturers to anticipate potential quality issues before they manifest or become significant. It allows them to promptly develop and implement preventative measures to maintain consistent product quality and reputation24.
Supply Chain Optimisation
Data analytics plays a crucial role in optimising manufacturers' supply chain operations. Manufacturers can identify inefficiencies and bottlenecks by leveraging data from various sources, including inventory levels, shipment times, and supplier performance, leading to reduced lead times, lower costs, and improved customer satisfaction23.
The use of data analytics in supply chain management enables organisations to achieve several benefits, such as enhanced efficiency and performance, improved decision-making, and increased visibility into operations. It also identifies areas for optimisation and improvement within the supply chain34.
Data analytics tools can analyse vast amounts of data from multiple sources, offering insights that can be used to optimise supply chain operations. These tools enable companies to make proactive changes, such as shifting production methods and pursuing demand-based supply chains, ultimately leading to a competitive advantage34.
Data analytics can optimise supply chain operations, inventory management, demand forecasting, logistics, and overall decision-making efficiency. It also helps mitigate risks and disruptions by providing real-time insights and enhancing transparency within the supply chain45.
Workforce Optimisation
Data analytics can significantly contribute to optimising the manufacturing workforce. By analysing employee performance, engagement, and other workforce-related factors, organisations can make more informed decisions about managing their employees, improving overall performance, and achieving their business objectives. Some key workforce optimisation strategies in people analytics include identifying key performance indicators (KPIs) for the workforce, collecting and analysing data, developing targeted interventions, and monitoring and adjusting interventions23.
Predictive analytics is also a game-changer for manufacturing workforce optimisation. It can identify potential skill gaps before they impact production, analyse trends, and predict future requirements, enabling proactive training and development planning3By analysing customer data, manufacturers can identify trends and patterns that inform product design, pricing strategies, and promotional activities4. Integrating predictive analytics in workforce management leads to a holistic improvement in operational efficiency, providing a significant competitive advantage34.
Workforce optimisation (WFO) is a set of strategies and practices to improve employee and organisational efficiency and decrease operational costs. WFO software combines analytics, quality management, call recording, coaching, speech analytics, text analytics, surveying, and feedback to optimise workforce processes45. Manufacturers can leverage workforce data to gain insight into labor productivity and personnel costs at each production stage. By analysing this data, manufacturers can make informed decisions about staffing levels, scheduling, and training programs to improve overall efficiency and reduce costs associated with labor turnover45.
Customer Insights
Data analytics can give manufacturers valuable customer insights, enabling them to understand customer preferences and behavior. Manufacturers can identify trends and patterns that inform product design, pricing strategies, and promotional activities by analysing customer data about how to serve customers best. This helps to improve customer satisfaction and loyalty, ultimately driving business growth23.
Customer insights are essential for manufacturers to develop targeted marketing campaigns and improve product development. By leveraging consumer data, manufacturers can better understand their customers' behaviors, preferences, and needs. This allows for more personalised and tailored customer interactions, increasing customer satisfaction and improved business outcomes34.
In today's competitive retail landscape, customer insights are crucial for providing high-quality experiences and products. By harnessing the power of consumer insights, manufacturers can make more informed decisions about how to serve their customers best and win over new ones45.
Overall, customer insights obtained through data analytics are fundamental in providing valuable information to help businesses exceed customer expectations, improve product development, and drive business growth. By leveraging consumer data, manufacturers can make more informed decisions on how to serve their customers best and win over new ones45.
Benefits of Data Analytics in Manufacturing
One of the key concerns when implementing data analytics in the manufacturing process is data quality. The success of any data analytics initiative relies heavily on the availability of accurate and reliable data. Manufacturers must ensure that the data collected is consistent, complete, and high-quality. Inconsistent or incomplete data can lead to flawed analysis and erroneous insights, rendering the entire data analytics effort ineffective. Organisations can implement robust data collection mechanisms to address this concern, invest in data cleansing and validation processes, and establish data governance practices to maintain data integrity23.
Another crucial concern is data security. Manufacturers deal with sensitive information related to production processes, trade secrets, and customer data. As data analytics involves collecting and analysing vast amounts of data, it becomes imperative to establish robust cybersecurity measures to protect against potential breaches or unauthorised access. Data encryption, access controls, regular security audits, and employee training on data security best practices are some measures manufacturers can adopt to safeguard their data and maintain the trust of their stakeholders23.
Despite these concerns, the benefits of applying data analytics in manufacturing are substantial. Improved efficiency is one of the primary advantages. By leveraging data analytics, manufacturers can identify bottlenecks, optimise production schedules, and streamline workflows. For example, by analysing historical production data, organisations can identify patterns and optimise machine maintenance schedules, reducing downtime and maximising productivity. Additionally, predictive analytics can help forecast demand accurately, enabling manufacturers to optimise inventory levels and reduce the risk of stockouts or overstocking23.
Cost reduction is another significant benefit of data analytics for the manufacturing industry. By identifying inefficiencies and optimising processes, manufacturers can reduce operational costs. For instance, data analytics can uncover energy consumption patterns, allowing organisations to optimise energy usage and reduce utility costs. Furthermore, predictive maintenance, made possible through data analytics, can help prevent equipment failures, reduce maintenance costs, and minimise unplanned downtime23.
In addition to efficiency and cost reduction, data analytics enables manufacturers to enhance product quality. Organisations can proactively address issues and minimise defects by analysing production data and identifying quality patterns. Real-time monitoring of production processes and analytics can provide early warning signals, allowing manufacturers to take corrective actions promptly. This improves product quality, enhances customer satisfaction, and reduces the need for costly rework or recalls23.
How to Leverage Data Analytics?
Data analytics has revolutionised various industries, and manufacturing is no exception. With the increasing use of IoT devices, automation tools, and other technologies, manufacturers generate vast amounts of data daily. This data provides valuable insights into production processes, supply chain management, product quality, and customer preferences. This article will explore how manufacturers can apply data analytics to improve operations, increase efficiency, and drive business growth12345.